2019.01.21
ステンレス板金
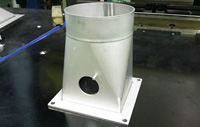
SUSホッパー
US304、t3mmにて製作。曲げと溶接による板金製品。
【お客様のご希望】
美観と製品寸法公差を保ちつつ、短納期にて対応を依頼。
【製作時のポイント】
寸法精度を出すために展開から曲げ加工まで細かく調整を行った。
溶接はフル溶接の仕様だったので、溶接手順やビード幅に注意し、製作した。
スクリューコンベア
食品粉体メーカー向けのスクリューコンベアです。
製作時にスクリューのピッチ、溶接等品質に注意しながら進める必要がある製品です。
【お客様のご希望】
スクリュー部の寸法公差、溶接部の荒さ等、製作物の品質に影響のないようにしてほしい。
【製作時のポイント】
スクリューの展開~曲げまで寸法の微調整を行い、溶接時もシャフトに合わせ開きを確認しながら慎重に行った。全体の溶接量に対しての縮みも考慮しながら製作を行った。
SUS洗浄容器
飲料を作る工程で用いる用具類を洗浄する容器。顧客から希望する形状と寸法のアウトラインをいただき、打合せから簡易な構造設計を行い、製作した。
【お客様のご希望】
3層1体型の容器でそれぞれ違う液体が入るので、別々で排水できるようにしてほしい。各層に取り付けるカゴも取り出しやすい位置にしたい。
【製作時のポイント】
3層それぞれの溶接箇所の気密性及び水圧による、製品側面のふくらみを防ぐため要所ごとに補強を追加し、対策を行った。
SUSブラケット、小物板金
板厚、表面処理等様々な種類の小物板金製品。機械に組み込む部品等なので精度、美観はもちろんコスト面でも顧客のニーズに対応できる品質が必要です。
【製作時のポイント】
大きさや形状の複雑さに応じて加工種類を使い分けた。
精度のいるものや形状の出しにくいものはレーザーを使い、高品質、高精度を遵守した。
簡単な形状、単発的な加工種類のものはシャーリング、セットプレス、プレスブレーキ等にて低コストで、なおかつ高い品質を迅速に製作した。
シュート
角がすべてR仕上がりになっているシュート。板厚がt2と薄いので溶接歪みと強度に注意が必要。
【お客様のご希望】
試験的に製作するので、一定の精度を保ってほしい。溶接箇所を原料滑降部に持ってこないようにしてほしい。自社での試験製作品なのでコスト面でも協力してほしい。
【製作時のポイント】
精度を保つため溶接箇所、溶接量を顧客と相談の上、極力減らし、歪みの影響がでないようにし、なおかつ強度面では十分な強度を保てる量を行った。展開時の板分割、角R部の変更をお客様に依頼し、製作工数の削減を図り、コストカットを行った。
排出ホッパー
角度のついた角丸ホッパー。下のストレート部と角丸のつなぎストレート部とR部の接続に精度が望まれる製品。
【お客様のご希望】
ホッパーの角度、寸法を遵守してほしい。各部品接続部の仕上がりの美観を重視し、スキマによる肉盛肥大等が、ないようにしてほしい。
【製作時のポイント】
小さく角度のついた角丸ホッパーなので展開と曲げに重点を置き、精密な加工を行いました。
溶接時にも無理やり取り付けるのではなく、ある程度精度よく取り付くよう、各単体で寸法をしっかり出すように心がけた。
ダストボックス
蓋開閉式のダストボックス。表面は全面ヘアライン仕上げ。側面のR部、蓋とのスキマの均一感の精度を意識し、美観を最重要視させた商品。
【お客様のご希望】
美観をとにかく重視するので、内面の溶接にも注意し表面に影響のないようにしてほしい。一切の妥協を許さず、確実に仕上げてほしい。
【製作時のポイント】
形状の精度を出すために展開、ロール加工に注意し、蓋と本体を現合にて照らし合わせながら加工を行った。表面に溶接焼け、裏面の膨らみを極力出さないよう、電流を細かく調整した。加工段階の傷をなくすため、部分加工終了後やロール加工時に表面にビニールを貼り直すようにした。
アルミケーブルダクト
リベットでの固定構造なので、1部品ごとの精度を意識する必要がある。フレームは溶接構造なので、歪みの影響に注意が必要。
【お客様のご希望】
組付け完了後の精度、突合せ部の板のスキマ等ないように加工してほしい。表面の美観に注意してほしい。
【製作時のポイント】
リベット構造なので、フレームと外板の穴合わせを現合にて加工し、確実に合わせれるようにした。
フレーム溶接時、アルミ材なので熱の影響に留意しながら歪みのないよう調整しながら施行した。
傷のないようにするため、ビニールを加工終了まで表面に貼り付けした。